Tags
How emerging technologies in the rice mill industry are embracing efficiency, precision, and sustainability
By Vasu Naren
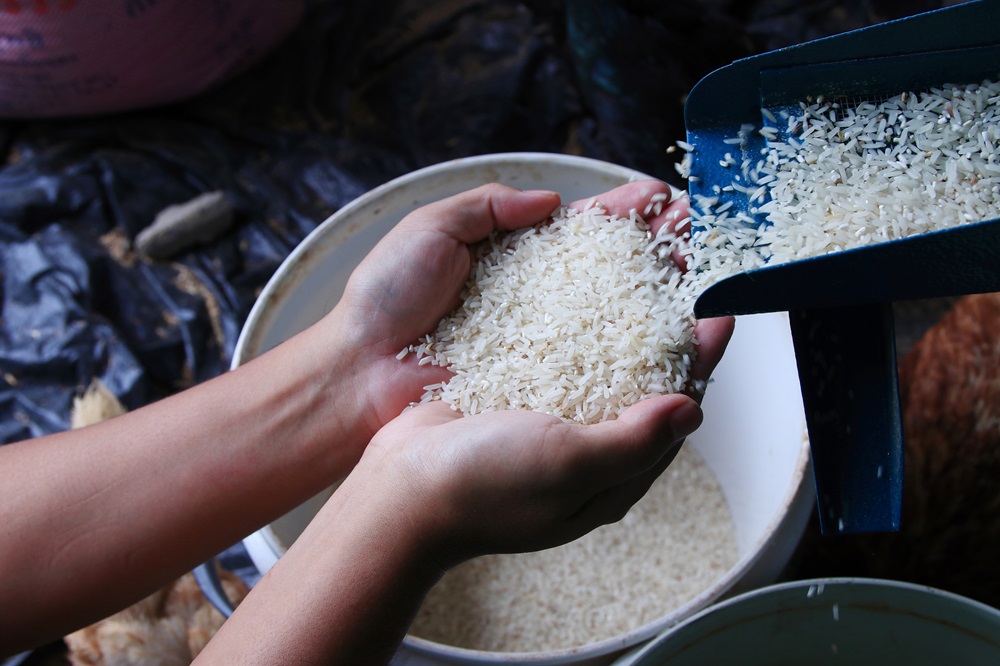
There is a phenomenal growth in the Rice market which roughly amounts to USD 102.80bn (report by Statista). The market is expected to grow annually by 7.60% (CAGR 2024-2029). These figures are a clear indication of the rapid growth of the rice milling industry globally, this is complimented by the rapidly evolving new technologies that are reshaping how we approach efficiency, precision, and sustainability. Advanced machinery and integrated digital solutions are enhancing every step of the process, from cleaning and hulling to polishing and packaging. Here’s how technology is driving the future of rice milling:
IoT Integration, Automation, and Data-Driven Efficiency with Advanced Sensors: Modern rice milling machines utilize IoT connectivity, automation, and advanced sensor technologies to revolutionize operational efficiency and product quality. IoT-enabled systems provide real-time monitoring of machine performance, production metrics, and maintenance needs, enabling predictive maintenance and minimizing downtime through timely alerts and adjustments. Advanced automation streamlines critical milling stages such as cleaning, dehusking, and polishing, with self-adjusting mechanisms ensuring precision and reducing manual intervention.
The integration of diverse sensor technologies enhances system performance and quality control:
- Optical Sensors: Use light to measure properties such as organic matter and moisture content. Photodiodes and photodetectors ensure precise calibration during milling processes.
- Mechanical Sensors: Probes measure resistance and compaction levels, optimizing the force applied during dehusking and polishing.
- Electrochemical Sensors: Detect specific ions, such as nitrogen, phosphorus, and potassium (NPK), ensuring optimal quality in processing. Ion-selective electrodes (ISE) and field-effect transistor sensors enhance detection accuracy.
- Dielectric Soil Moisture Sensors: Measure dielectric constants to assess moisture levels, which is crucial for rice quality. Frequency domain reflectometry (FDR) or time domain reflectometry (TDR) ensures consistent grain moisture levels.
- Airflow Sensors: Evaluate air permeability to monitor compaction, moisture, and structural integrity during processing.
- Location Sensors (GPS): Ensure precise tracking of production logistics by determining latitude, longitude, and altitude, pivotal for efficient inventory and supply chain management.
Incorporating high-speed cameras and spectral confocal systems, these machines achieve enhanced precision, real-time performance adjustments, and superior quality control. Integrated data analytics allow for continuous tracking of output, machine performance, and quality metrics, empowering operators to make informed decisions, optimize resources, and deliver consistent, high-quality rice products.
Sustainable Processing Technologies
- Energy-Efficient Motors and Equipment: To address the environmental impact, rice mills are adopting energy-efficient motors and processing equipment that reduce electricity consumption. These technologies help lower operating costs and reduce the carbon footprint, meeting global sustainability standards.
- Water and Waste Management Systems: Some machines are equipped with systems that use less water during the milling process and can recycle byproducts such as rice husks and bran. By leveraging these eco-friendly options, rice mills can reduce water consumption and waste production, aligning with modern sustainability practices.
Green Energy Adoption in the Rice Milling Industry: The rice milling industry is increasingly integrating green energy systems to achieve sustainability and energy efficiency. Two primary methods of energy production—gasification and direct combustion—are widely employed, utilizing rice husk and other agricultural residues as biomass fuels:
Gasification:
- This process converts biomass (e.g., rice husk, groundnut shells, pigeon pea stalks) into producer gas, a combustible gas mixture.
- The gasification process involves carbon oxidation, CO2 reduction, H2 release, and CH4 formation, achieving an efficiency of 70–80%.
- Coupled with a thermal engine and alternator, it generates electricity with an overall efficiency of 93%. For instance, 0.55 lb (25 g) of diesel fuel and 2,200 kcal of gaseous energy can produce 1 kWh (3.6 MJ) of electricity.Direct Combustion:
- Solid fuels like rice husk are burned directly, producing both gaseous substances (volatile matter) and solid residue (carbon and ash).
- Approximately 200 kg of rice husk from milling one tonne of paddy can generate 660 kg of steam, producing 100 kWh of electricity via a steam turbine.
- Excess air is supplied to ensure complete combustion, maximizing energy output while reducing waste.
These systems not only reduce dependence on fossil fuels but also utilize agricultural byproducts effectively, creating a self-sustaining energy loop within rice mills. By adopting such green energy solutions, rice mills can minimize carbon footprints, lower energy costs, and contribute to a cleaner environment.
Advanced Technologies for Raw Material Management in Rice Mills
- Modern rice mills employ advanced technologies to optimize raw material management, ensuring efficiency and product quality:
- Automated Sorting Systems: Remove impurities such as damaged or discolored grains, enhancing product consistency.
- Conveyor Belts: Facilitate seamless transport of raw materials throughout the production line, reducing manual handling.
- Moisture Meters: Assess moisture levels to determine if materials require additional drying, ensuring readiness for processing.
- Sensors: Monitor machine performance, predict maintenance needs, and analyze how machine settings impact quality, minimizing downtime and maximizing efficiency.
- ERP Systems: Streamline purchase and inventory management, providing real-time insights into raw material availability and operational planning.
These technologies collectively improve operational efficiency, reduce waste, and ensure high-quality output in rice milling.
Conclusion
Technological advancements are transforming the rice milling industry, offering a pathway to greater efficiency, enhanced precision, and a sustainable future. From AI-driven sorting to IoT-enabled monitoring, these technologies provide a competitive edge in an evolving market. As rice mills embrace these innovations, they not only enhance production quality and reduce environmental impact but also set the stage for a highly automated, future-ready industry that meets the demands of an ever-growing global population.
https://etedge-insights.com/industry/manufacturing/how-emerging-technological-trends-in-the-rice-mill-industry-is-embracing-efficiency-precision-and-sustainability/Published Date: December 16, 2024